Trailer Hub Removal
Whenever the hub equipment on your axle must be removed for
inspection or maintenance the following procedure should be utilized.
- Elevate and support the trailer unit per manufacturers' instructions.
- Remove the wheel.
- Remove the grease cap by carefully prying progressively around the flange of the cap. If the hub is an oil lube type, then the cap can be removed by unscrewing it counter- clockwise while holding the hub stationary.
- Remove the cotter pin from the spindle nut or, in the case of E-Z Lube versions, bend the locking tang to the free position.
- Unscrew the spindle nut (counterclockwise) and remove the spindle washer.
- Remove the hub from the spindle, being careful not to allow the outer bearing cone to fall out. The inner bearing cone will be retained by the seal.
- On 7200# and 8000# a hub puller should be used to assist drum removal.
Trailer Brake Drum Inspection
There are two areas of the brake drum that are subject to wear and require periodic inspection. These two areas are the drum
surface where the brake shoes make contact during stopping and the armature surface where the magnet contacts (only in electric
brakes.)
The drum surface should be inspected for excessive wear or heavy scoring. If worn more than .020" oversized, or the drum
has worn out of round by more than .015", then the drum surface should be turned. If scoring or other wear is greater than .090" on
the diameter, the drum must be replaced. When turning the drum surface, the maximum rebore diameter is as follows:
- ยท7" Brake Drum-7.090"
- 10" Brake Drum-10.090"
- 12" Brake Drum-12.090"
- 12'/4" Brake Drum-12.340"
The machined inner surface of the brake drum that contacts the brake magnet is called the armature surface. If the armature
surface is scored or worn unevenly, it should be refaced to a 120 micro inch finish by removing not more than .030" of material. To
insure proper contact between the armature face and the magnet face, the magnets should be replaced whenever the armature
surface is refaced and the armature surface should be refaced whenever the magnets are replaced.
Note: It is important to protect the wheel bearing bores from metallic chips and
contamination which result from drum turning or armature refacing operations.
Make certain that the wheel bearing cavities are clean and free of contamination before
reinstalling bearing and seals. The presence of these contaminants will cause premature Bearing race or cup
wheel bearing failure.
Caution: Be sure to wear safety glasses when removing or
installing forced fitted parts. Failure to comply may result in
serious eye injury.
Trailer Bearing Inspection
Wash all grease and oil from the bearing cone using a suitable solvent. Dry the bearing with a clean, lint-free cloth and inspect
each roller completely. If any pitting, spalling, or corrosion is
present, then the bearing must be replaced. The bearing cup inside the hub must be inspected.
IMPORTANT: Bearings must always be replaced in sets of a cone and a cup.
When replacing the bearing cup proceed as
follows:
- Place the hub on a flat work surface with the cup to be replaced on the bottom side.
- Using a brass drift punch, carefully tap around the small diameter end of the cup to drive out.
- After cleaning the hub bore area, replace the cup by tapping in with the brass drift punch. Be sure the cup is seated all the way up against the retaining shoulder in the hub.
Trailer Bearing Lubrication
Along with bearing adjustment, proper lubrication is essential to the current function and reliability of your trailer axle. Bearings
should be lubricated every 12 months or 12,000 miles. The method to repack bearing cones is as follows:
- Place a quantity of grease into the palm of your hand.
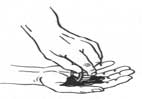
- Press a section of the widest end of the bearing into the
outer edge of the grease pile closest to the thumb forcing
grease into the interior of the bearing.
- Repeat this while rotating the bearing from roller to roller.
- Continue this process until you have the entire bearing
completely filled with grease.
- Before reinstalling, apply a light coat of grease on the
bearing cup.
|